Rubber
Petroleum resin, as a rubber additive, can replace traditional cumarone resin, enhancing viscosity and improving the blending and extrusion performance. Petroleum resins with lower softening points can be used as plasticizers for rubber, while those with higher softening points can serve as reinforcing agents. Light-colored petroleum resins are suitable for producing colored rubber, while dark-colored resins are suitable for black rubber.
Rubber mainly utilizes low softening point C5 petroleum resin, C5/C9 copolymer resin, and DCPD resin. Such resins exhibit excellent compatibility with natural rubber particles, having minimal impact on the rubber vulcanization process. The addition of petroleum resins to rubber serves to enhance tackiness, reinforce, and soften the rubber. In particular, the inclusion of C5/C9 copolymer resin not only increases the cohesion between rubber particles but also enhances the adhesion between rubber particles and tire cords, making it suitable for high-performance rubber products like radial tires.
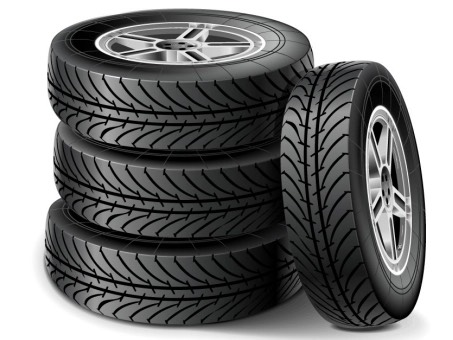
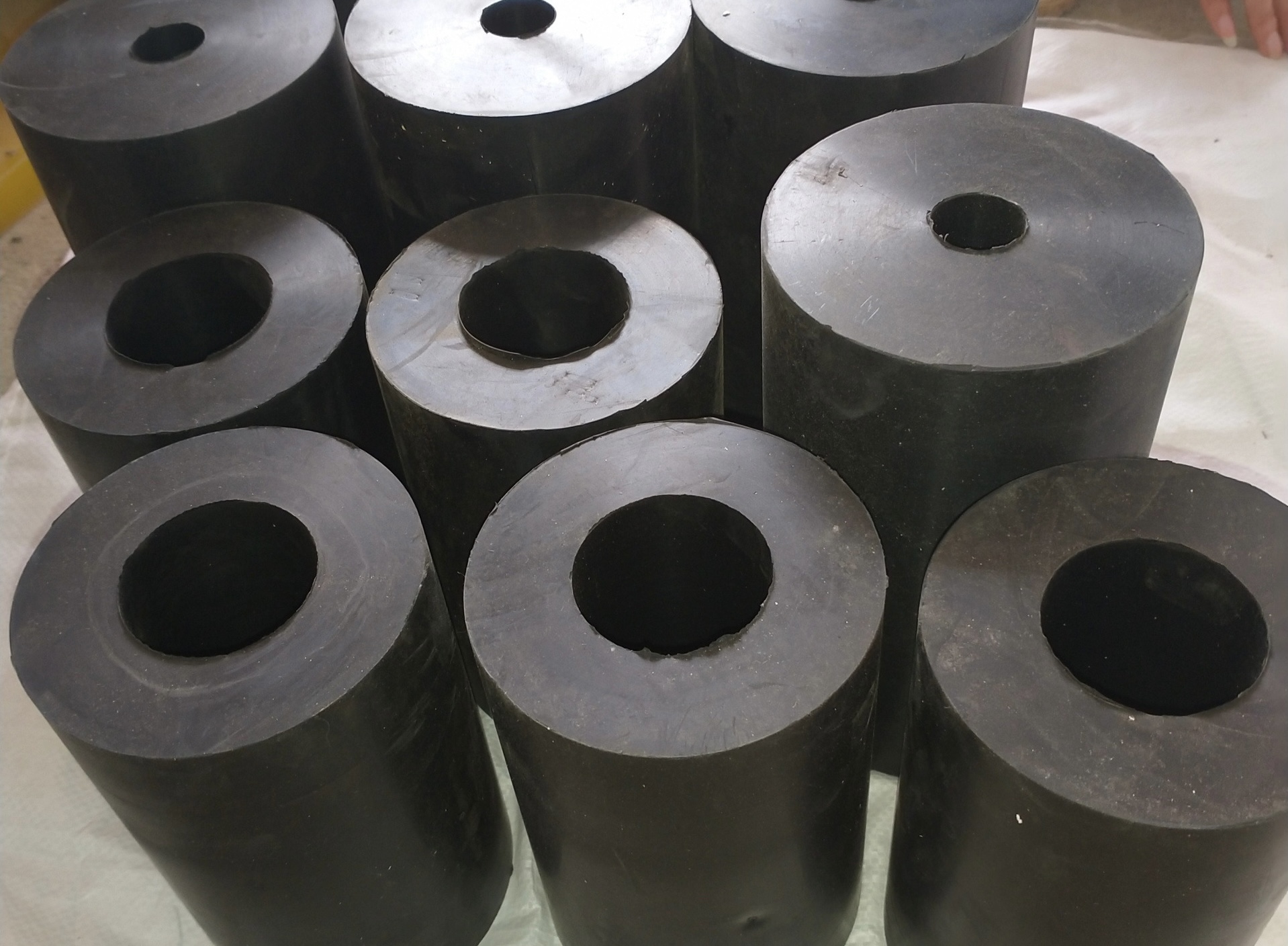